精密配件的铸造工艺有哪些?
精密配件,指装配机械的零件或部件;或损坏后重新安装上的零件或部件。配件可以分为两类:标准配件和可选配件;今天我们来讲一讲各种精密配件的铸造工艺。
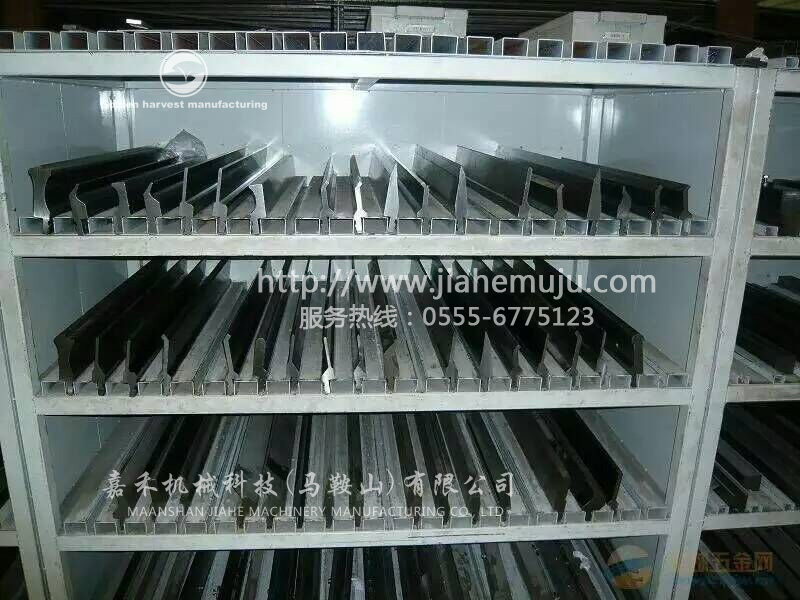
一、精密塑性成形
精密塑性加工技术在工业发达国家受到高度重视,并投入大量资金优先发展。70年代美国空军主持制订“锻造工艺现代化计划”,目的是使锻造这一重要工艺实现现代化,更多地使用CAD/CAM,使新锻件的制造周期减少75%。1992年,美国国防部提出了“军用关键技术清单”,其中包含了等压成型工艺、数控计算机控制旋压、塑变和剪切成形机械、超塑成型/扩散连接工艺、液压延伸成型工艺等精密塑性成型工艺。此外,国外近年来还发展了以航空航天产品为应用对象的“大型模锻件的锻造及叶片精锻工艺”、“快速凝固粉末层压工艺”、“大型复杂结构件强力旋压成型工艺”、“难变形材料超塑成形工艺”、“先进材料(如金属基复合材料、陶瓷基复合材料等)成形工艺''等。近来,随着计算机和自动化技术对热加工成形工艺的渗透,板材成形柔性制造系统也开始崭露头角。
二.超塑成形
美国休斯公司、 BAE公司等在超塑成形技术方面居世界前列。目前钦合金超塑成形工艺已广泛用于制造导弹外壳,推进剂储箱,整流罩、球形气瓶、波纹板及发动机部件等。铝合金、镁合金、镍基高温合金、金属基复合材料等的超塑成形工艺也在研究。我国的超塑成形技术在航天航空及机械行业已有应用,如航天工业中的卫星部件、导弹和火箭气瓶等,并采用超塑成形法制造侦察卫星的钦合金回收舱。与此同时,还基本上掌握了锌、铜、铝、钦合金的超塑成形工艺,最小成形厚度可达0.3mm,形状也较复杂。但壁厚均匀性问题尚待解决。
三.强力旋压
美国利用强力旋压精密配件技术。已能生产直径为3.9m、径向尺寸精度0.05mm、表面粗糙度Ra0.16—0.32μm、壁厚差<0.03mm的导弹壳体。几乎对各种金属均能旋压成形,且工艺稳定,并已实现设备大型化,多用途化和自动化。错距旋压、CNC等先进旋压工艺及设备也已普及使用。
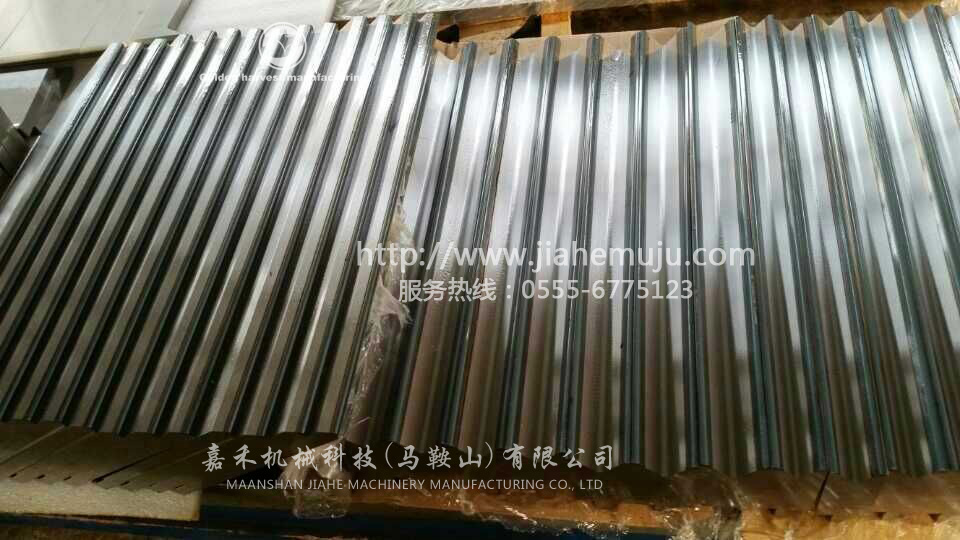
四、精密铸造
精密铸造成形工艺不但可以缩短新型武器的研制周期、降低成本,还可以提高武器的灵活性、可靠性。如美国波音公司生产的巡航导弹的舱体采用铝合金精密铸造工艺后,弹体成本降低30%,每枚导弹所需工时从8000小时减少到5500小时,且可靠性提高,重量有所降低。
美国橡树岭国家实验室、美国精密铸造公司和NASA刘易斯研究中心等单位对A1系金属间化合物和Ti、
Ni基等特种合金的精密铸造进行了大量研究。他们采用整体一次成形精铸工艺加工涡喷、涡扇导向器,减少机加工时40%,成本降低30%。我国军工系统的精密铸造工艺与国外相比差距较大。如导弹舱体主要采用低、差压铸造法。普通粘土砂铸型生产舱段,尺寸精度低,表面质量较差,内部缺陷多,合金液二次氧化严重,力学性能不高,废品率高达20%-30%,目前国内仅能铸造1.4m以下的舱段。另外象导弹尾翼、飞机部分器件等仍采用机械加工方法,不但生产周期长、成本高,而且可靠性也较差。在特种合金精密铸造工艺方面,同样存在很大差距,象单品空心无余量叶片精铸工艺,在国外已应用于军工生产,而国内尚处于研究阶段。至于A1系金属间化合物的精密铸造工艺的研究目前还未开。 综上所述,与国外相比,我国在精密铸造工艺方面约落后10-15年。为了缩短新型武器的研制和生产周期、降低成本、提高可靠性,必须加强精密铸造工艺的研究。
由于我国汽车配件制造行业起步晚、起点低、产业结构不合理。改革开放以来,汽车配件制造行业虽有了较快发展,但与汽车生产大国相比,差距仍然明显。特别是与国外配件制造企业相比,差距更为明显。我国汽车配件制造行业的差距,除了规模上的差距,更重要的是制造技术以及管理技术上的差距;马鞍山嘉禾机械科技有限公司专业从事折弯模具,数控折弯模具,生产线配件,精密配件,模具/配件加工,优良的设备,精湛的工艺,严格的检验,完善的售后服务.联系电话:18005552119
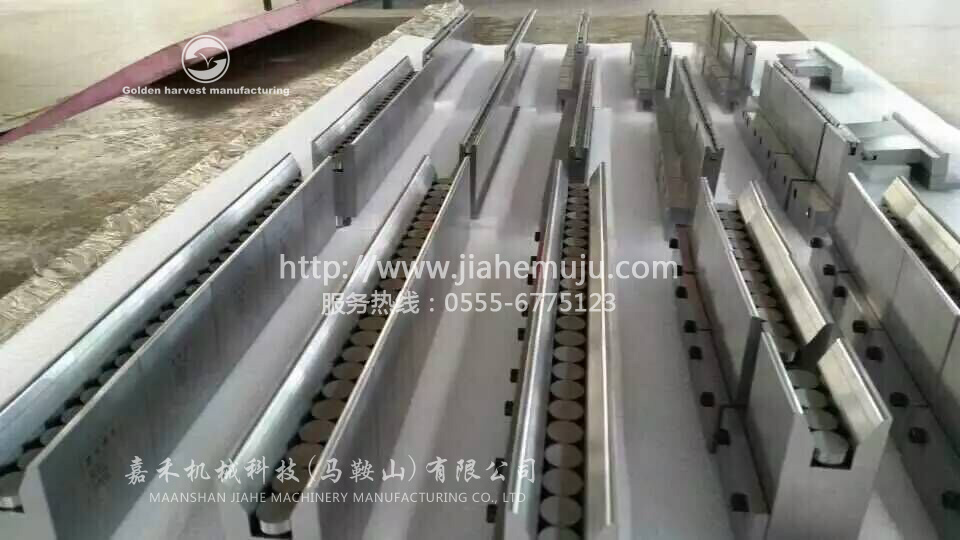
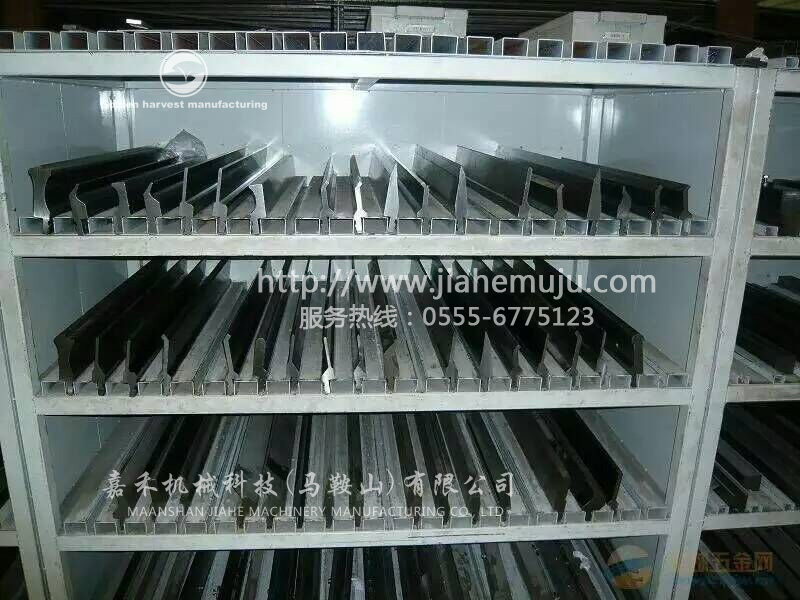
一、精密塑性成形
精密塑性加工技术在工业发达国家受到高度重视,并投入大量资金优先发展。70年代美国空军主持制订“锻造工艺现代化计划”,目的是使锻造这一重要工艺实现现代化,更多地使用CAD/CAM,使新锻件的制造周期减少75%。1992年,美国国防部提出了“军用关键技术清单”,其中包含了等压成型工艺、数控计算机控制旋压、塑变和剪切成形机械、超塑成型/扩散连接工艺、液压延伸成型工艺等精密塑性成型工艺。此外,国外近年来还发展了以航空航天产品为应用对象的“大型模锻件的锻造及叶片精锻工艺”、“快速凝固粉末层压工艺”、“大型复杂结构件强力旋压成型工艺”、“难变形材料超塑成形工艺”、“先进材料(如金属基复合材料、陶瓷基复合材料等)成形工艺''等。近来,随着计算机和自动化技术对热加工成形工艺的渗透,板材成形柔性制造系统也开始崭露头角。
二.超塑成形
美国休斯公司、 BAE公司等在超塑成形技术方面居世界前列。目前钦合金超塑成形工艺已广泛用于制造导弹外壳,推进剂储箱,整流罩、球形气瓶、波纹板及发动机部件等。铝合金、镁合金、镍基高温合金、金属基复合材料等的超塑成形工艺也在研究。我国的超塑成形技术在航天航空及机械行业已有应用,如航天工业中的卫星部件、导弹和火箭气瓶等,并采用超塑成形法制造侦察卫星的钦合金回收舱。与此同时,还基本上掌握了锌、铜、铝、钦合金的超塑成形工艺,最小成形厚度可达0.3mm,形状也较复杂。但壁厚均匀性问题尚待解决。
三.强力旋压
美国利用强力旋压精密配件技术。已能生产直径为3.9m、径向尺寸精度0.05mm、表面粗糙度Ra0.16—0.32μm、壁厚差<0.03mm的导弹壳体。几乎对各种金属均能旋压成形,且工艺稳定,并已实现设备大型化,多用途化和自动化。错距旋压、CNC等先进旋压工艺及设备也已普及使用。
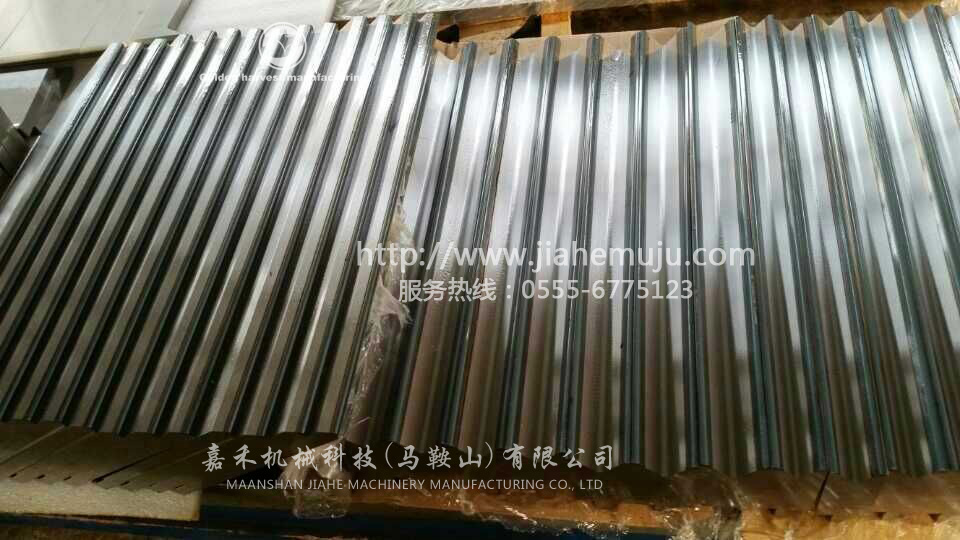
四、精密铸造
精密铸造成形工艺不但可以缩短新型武器的研制周期、降低成本,还可以提高武器的灵活性、可靠性。如美国波音公司生产的巡航导弹的舱体采用铝合金精密铸造工艺后,弹体成本降低30%,每枚导弹所需工时从8000小时减少到5500小时,且可靠性提高,重量有所降低。
美国橡树岭国家实验室、美国精密铸造公司和NASA刘易斯研究中心等单位对A1系金属间化合物和Ti、
Ni基等特种合金的精密铸造进行了大量研究。他们采用整体一次成形精铸工艺加工涡喷、涡扇导向器,减少机加工时40%,成本降低30%。我国军工系统的精密铸造工艺与国外相比差距较大。如导弹舱体主要采用低、差压铸造法。普通粘土砂铸型生产舱段,尺寸精度低,表面质量较差,内部缺陷多,合金液二次氧化严重,力学性能不高,废品率高达20%-30%,目前国内仅能铸造1.4m以下的舱段。另外象导弹尾翼、飞机部分器件等仍采用机械加工方法,不但生产周期长、成本高,而且可靠性也较差。在特种合金精密铸造工艺方面,同样存在很大差距,象单品空心无余量叶片精铸工艺,在国外已应用于军工生产,而国内尚处于研究阶段。至于A1系金属间化合物的精密铸造工艺的研究目前还未开。 综上所述,与国外相比,我国在精密铸造工艺方面约落后10-15年。为了缩短新型武器的研制和生产周期、降低成本、提高可靠性,必须加强精密铸造工艺的研究。
由于我国汽车配件制造行业起步晚、起点低、产业结构不合理。改革开放以来,汽车配件制造行业虽有了较快发展,但与汽车生产大国相比,差距仍然明显。特别是与国外配件制造企业相比,差距更为明显。我国汽车配件制造行业的差距,除了规模上的差距,更重要的是制造技术以及管理技术上的差距;马鞍山嘉禾机械科技有限公司专业从事折弯模具,数控折弯模具,生产线配件,精密配件,模具/配件加工,优良的设备,精湛的工艺,严格的检验,完善的售后服务.联系电话:18005552119
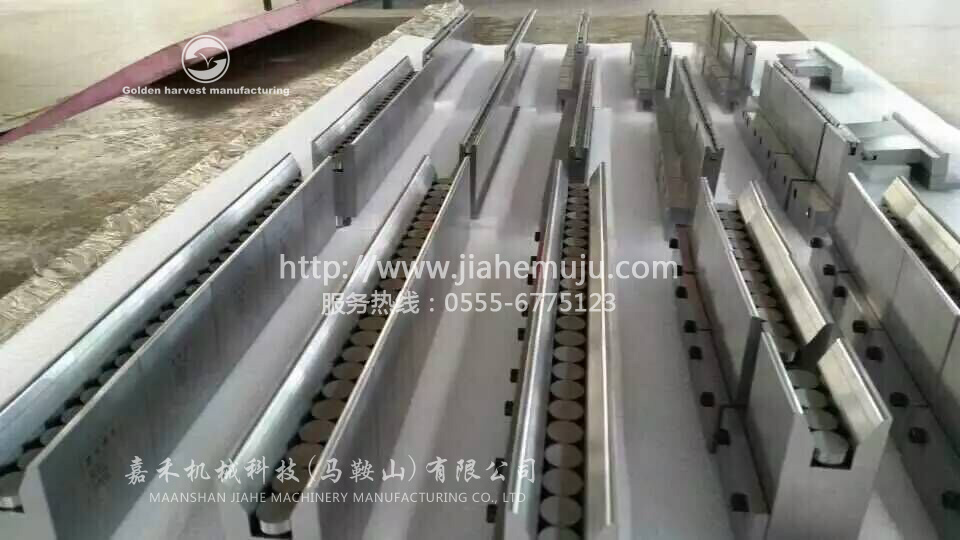